Abrasive Blasting
Abrasive blasting, also known as sandblasting, is a process in which abrasive materials are propelled at high velocity against a surface. The objective is to smooth, shape, or remove surface contaminants from the target material. The abrasive material is typically a granular substance with abrasive properties.
Here are the key components and aspects of abrasive blasting:
1. Abrasive Material: Various abrasive materials can be used in blasting, depending on the desired outcome and the material being treated. Common abrasives include sand, steel grit, aluminum oxide, glass beads, and walnut shells, among others. The choice of abrasive depends on factors such as hardness, particle size, and the specific application.
2. Blasting Equipment: Abrasive blasting is carried out using specialized equipment. The most common types include:
- Blast Cabinet: A closed environment where the blasting occurs, protecting the operator and surrounding area from abrasive materials.
- Blast Room: Similar to a blast cabinet but larger, suitable for more extensive work.
- Portable Blasting Systems: Mobile units that can be moved to the work site.
3. Compressed Air or Water: Abrasive materials are propelled using either compressed air or water. Compressed air is the most common method, where the abrasive is mixed with air in a blasting pot and then expelled through a nozzle at high speed.
4. Nozzle: The nozzle is a critical component as it controls the flow and velocity of the abrasive material. Nozzles are designed for different applications and may be constructed from materials that resist wear caused by the abrasive particles.
5. Surface Preparation: Abrasive blasting is widely used for surface preparation in various industries. It can remove rust, scale, old paint, or other contaminants, preparing the surface for coating, painting, or further treatment.
6. Cleaning and Etching: In addition to preparing surfaces, abrasive blasting can be used for cleaning and etching materials. For example, it is used in cleaning automotive components, graffiti removal, or creating a matte finish on glass.
7. Safety Considerations: Safety is a crucial aspect of abrasive blasting. Operators must use personal protective equipment (PPE) such as helmets, gloves, and respiratory protection to prevent exposure to abrasive dust. The blasting environment must also be controlled to minimize the risk of harm to operators and bystanders.
8. Environmental Impact: The environmental impact of abrasive blasting includes concerns about dust emissions and the disposal of used abrasive materials. Proper containment and dust collection systems are often employed to mitigate these issues.
Abrasive blasting is a versatile and effective process used in various industries, including manufacturing, construction, automotive, and shipbuilding. While it provides numerous benefits, it requires careful consideration of safety and environmental factors to ensure responsible and sustainable use.
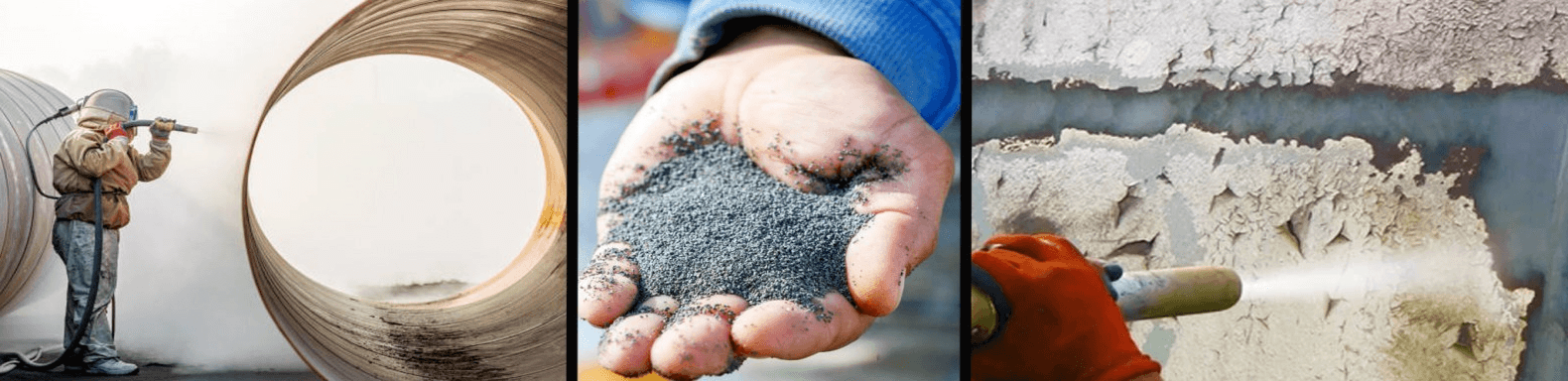