Adjustable parallel
An adjustable
parallel, also known as an adjustable parallel set or parallel bar set, is a
precision measuring tool used in machining and manufacturing processes. It
consists of a set of parallel bars or plates that can be adjusted in height to
provide precise and accurate spacing between two surfaces or workpieces. The
adjustable parallel set typically includes a number of parallel bars of
different sizes.
Here are some key features and uses of adjustable
parallels:
1. Adjustable Height: The main feature of adjustable parallels is the
ability to adjust the height of the parallel bars. This allows for precise
alignment and spacing between workpieces or machine parts.
2. Parallelism: The parallel bars in the set are manufactured to high
accuracy and maintain parallelism with each other. This ensures consistent
spacing and alignment across the entire set.
3. Measurement: Adjustable parallels are often used in conjunction with
other measuring tools such as calipers or micrometers to measure and set
precise distances between surfaces or workpieces.
4. Workpiece Support: Adjustable parallels can be used to support workpieces
during machining or inspection processes. They provide a stable and leveled
surface for accurate measurements and machining operations.
5. Machine Setup: Adjustable parallels are commonly used in machine setups
to align and position workpieces or tooling. They help ensure that the
workpiece is positioned correctly and parallel to the machine's axes.
6. Versatility: Adjustable parallels can be used in various machining
operations, including milling, drilling, grinding, and inspection. They are
suitable for both manual and CNC machining applications.
7. Durability and Material: Adjustable parallels are typically made from
hardened steel or other high-quality materials to ensure durability and
precision. Some sets may also have a surface treatment or coating for corrosion
resistance.
Adjustable parallels are valuable tools in precision
machining and manufacturing industries, allowing for accurate measurements,
alignment, and setup of workpieces. They provide flexibility and precision in
achieving parallelism and consistent spacing, contributing to high-quality and
precise machining operations.
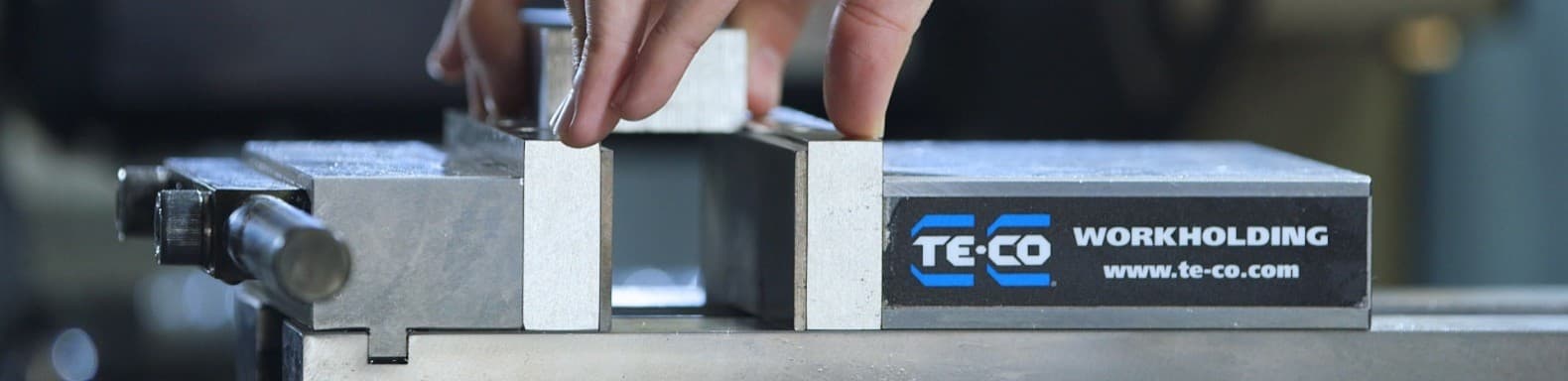